V-tail, five-passenger aircraft builds on the vison of the S-A1, designed with a priority on safety and a focus on sustainability.
Agreement with green hydrogen producer extended for 2024, investment will support ongoing global capacity expansions including CFRP cylinder production. DMC insulator
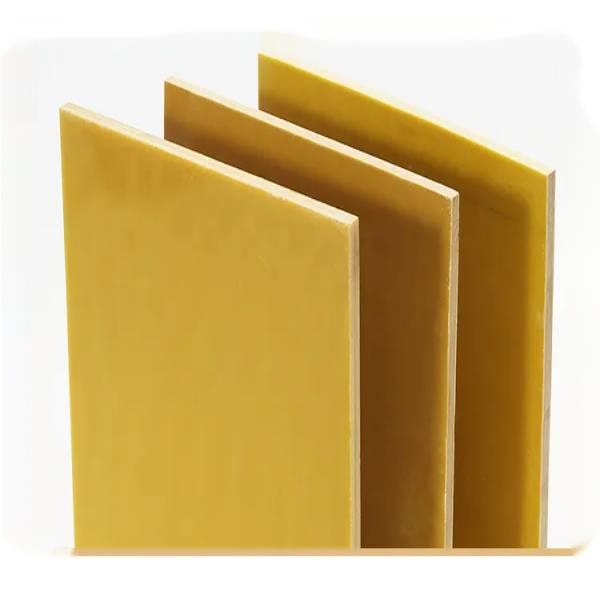
Multifunctional four-axis winding system offering fiber flexibility will underpin the NCC’s work in testing and manufacturing pressure vessels leading to commercial production.
The EHang unmanned aerial vehicle (UAV) complies with approved type design, safety and quality requirements, with deliveries to customers now underway.
Overair heads to flight testing in early 2024, marked by rapid prototype development.
The eVTOL developer is scouting locations in the U.S. for continued flight testing of its inaugural consumer aircraft, AIR One, through the Agility Prime program.
A new ASTM-standardized test method established in 2022 assesses the compression-loaded damage tolerance of sandwich composites.
Composites automation specialist increases access to next-gen technologies, including novel AFP systems and unique 3D parts using adaptive molds.
Combined LSAM and five-axis CNC milling capabilities will optimize D-Composites’ production services, flexibility and cut time and cost for composite tooling manufacture.
Evaluation of CFRTP m-pipe through Element’s U.K. facility aims to qualify the system for new operating environments.
Innovative prepreg tooling is highly drapable, capable of forming complex carbon fiber tooling shapes, in addition to reducing through thickness porosity and only requiring one debulk during layup.
Simutence and Engenuity demonstrate a virtual process chain enabling evaluation of process-induced fiber orientations for improved structural simulation and failure load prediction of a composite wing rib.
Maintaining high strength and tensile modulus exceeding 350 GPa has been achieved using Toray’s nano-level structural control technology.
Eco-friendly carbon fiber slashes carbon footprint by half through renewable energy, a commitment echoed in SGL’s Lavradio biomass plant set to reduce CO2 emissions by 90,000 tons.
JEC World 2024: Flax fiber producer Groupe Depestele and sustainable composites company Greenboats demonstrate flax fiber materials, demonstrators and product offer Circular Structures.
Flax fiber multiaxial reinforcement plies, a CNC milled wood core and bamboo rail sections are press molded together using Sicomin’s bio-epoxy resin system for an eco-friendly twintip kiteboard production.
In 2006, guest columnist Bob Hartunian related the story of his efforts two decades prior, while at McDonnell Douglas, to develop a thermoplastic composite crytank for hydrogen storage. He learned a lot of lessons.
Acrylonitrile to be used in Tenax uses waste and residue from biomass-derived products or recycled raw materials that are ISCC Plus certified, maintaining same performance properties as conventional-based products.
JEC World 2024: Endless Industries offers 3D printing customers integration of its proprietary printhead, software and fiber filaments to achieve the benefits of lightweight composite parts.
This compact cell brings together 3D printing, AFP and milling aided by a comprehensive software program, further simplifying the manufacture of complex thermoplastic composite aerostructures in the future.
In 2006, guest columnist Bob Hartunian related the story of his efforts two decades prior, while at McDonnell Douglas, to develop a thermoplastic composite crytank for hydrogen storage. He learned a lot of lessons.
Multifunctional four-axis winding system offering fiber flexibility will underpin the NCC’s work in testing and manufacturing pressure vessels leading to commercial production.
Named the NASA Government Invention of the Year, the 3D orthogonally woven materials supports structural and thermal performance needs for Orion mission and more.
Breiana Whitehead, pioneering Australian kite-foil sailor, spearheads board design intricacies with ATL Composites to enhance her performance ahead of the July 2024 competition.
CW explores key composite developments that have shaped how we see and think about the industry today.
Knowing the fundamentals for reading drawings — including master ply tables, ply definition diagrams and more — lays a foundation for proper composite design evaluation.
As battery electric and fuel cell electric vehicles continue to supplant internal combustion engine vehicles, composite materials are quickly finding adoption to offset a variety of challenges, particularly for battery enclosure and fuel cell development.
Performing regular maintenance of the layup tool for successful sealing and release is required to reduce the risk of part adherence.
Increasingly, prototype and production-ready smart devices featuring thermoplastic composite cases and other components provide lightweight, optimized sustainable alternatives to metal.
The composite pressure vessel market is fast-growing and now dominated by demand for hydrogen storage.
The burgeoning advanced air mobility (AAM) market promises to introduce a new mode of transport for urban and intercity travelers — particularly those who wish to bypass the traffic congestion endemic to the world’s largest cities. The electric vertical take-off and landing (eVTOL) aircraft serving this market, because they depend on battery-powered propulsion, also depend on high-strength, high-performance composite structures produced at volumes heretofore unseen in the aerospace composites industry. This CW Tech Days will feature subject matter experts exploring the materials, tooling and manufacturing challenges of ramping up composites fabrication operations to efficiently meet the demands of a challenging and promising new marketplace.
Manufacturers often struggle with production anomalies that can be traced back to material deviations. These can cause fluctuations in material flow, cooling, and cure according to environmental influences and/or batch-to-batch variations. Today’s competitive environment demands cost-efficient, error-free production using automated production and stable processes. As industries advance new bio-based, faster reacting and increased recycled content materials and faster processes, how can manufacturers quickly establish and maintain quality control? In-mold dielectric sensors paired with data analytics technology enable manufacturers to: Determine glass transition temperature in real time Monitor material deviations such as resin mix ratio, aging, and batch-to-batch variations throughout the process Predict the influence of deviations or material defects during the process See the progression of curing and demold the part when the desired degree of cure, Tg or crystallinity is achieved Document resin mix ratios using snap-cure resins for qualification and certification of RTM parts Successful case histories with real parts illustrate how sensXPERT sensors, machine learning, and material models monitor, predict, and optimize production to compensate for deviations. This Digital Mold technology has enabled manufacturers to reduce scrap by up to 50% and generated energy savings of up to 23%. Agenda: Dealing with the challenge of material deviations and production anomalies How dielectric sensors work with different composite resins, fibers and processes What is required for installation Case histories of in-mold dielectric sensors and data analytics used to monitor resin mixing ratios and predict potential material deviations How this Digital Mold technology has enabled manufacturers to optimize production, and improve quality and reliability
SolvaLite is a family of new fast cure epoxy systems that — combined with Solvay's proprietary Double Diaphragm Forming technology — allows short cycle times and reproducibility. Agenda: Application Development Center and capabilities Solutions for high-rate manufacturing for automotive Application examples: battery enclosures and body panels
OEMs around the world are looking for smarter materials to forward-think their products by combining high mechanical performance with lightweight design and long-lasting durability. In this webinar, composite experts from Exel Composites explain the benefits of a unique continuous manufacturing process for composites profiles and tubes called pull-winding. Pull-winding makes it possible to manufacture strong, lightweight and extremely thin-walled composite tubes and profiles that meet both demanding mechanical specifications and aesthetic needs. The possibilities for customizing the profile’s features are almost limitless — and because pull-winding is a continuous process, it is well suited for high volume production with consistent quality. Join the webinar to learn why you should consider pull-wound composites for your product. Agenda: Introducing pull-winding, and how it compares to other composite manufacturing technologies like filament winding or pultrusion What are the benefits of pull-winding and how can it achieve thin-walled profiles? Practical examples of product challenges solved by pull-winding
Composite systems consist of two sub-constituents: woven fibers as the reinforcement element and resin as the matrix. The most commonly used fibers are glass and carbon, which can be processed in plane or satin structures to form woven fabrics. Carbon fibers, in particular, are known for their high strength/weight properties. Thermoset resins, such as epoxies and polyurethanes, are used in more demanding applications due to their high physical-mechanical properties. However, composites manufacturers still face the challenge of designing the right cure cycles and repairing out-of-shelf-life parts. To address these issues, Alpha Technologies proposes using the encapsulated sample rheometer (premier ESR) to determine the viscoelastic properties of thermosets. Premier ESR generates repeatable and reproducible analytical data and can measure a broad range of viscosity values, making it ideal for resins such as low viscous uncured prepreg or neat resins as well as highly viscous cured prepregs. During testing, before cure, cure and after cure properties can be detected without removing the material from the test chamber. Moreover, ESR can run a broad range of tests, from isothermal and non-isothermal cures to advanced techniques such as large amplitude oscillatory shear tests. During this webinar, Alpha Technologies will be presenting some of the selected studies that were completed on epoxy prepreg systems utilizing ESR and how it solves many issues in a fast and effective way. It will highlight the advantages of this technique that were proven with the work of several researchers. Moreover, Alpha Technologies will display part of these interesting findings using the correlations between the viscoelastic properties such as G’ and mechanical properties such as short beam shear strength (SBS).
Surface preparation is a critical step in composite structure bonding and plays a major role in determining the final bonding performance. Solvay has developed FusePly, a breakthrough technology that offers the potential to build reliable and robust bonded composite parts through the creation of covalently-bonded structures at bondline interface. FusePly technology meets the manufacturing challenges faced by aircraft builders and industrial bonding users looking for improved performance, buildrates and lightweighting. In this webinar, you will discover FusePly's key benefits as well as processing and data. Agenda: Surface preparation challenges for composite bonding FusePly technology overview Properties and performance data
The annual Conference on Composites, Materials, and Structures (also known as the Cocoa Beach Conference) is the preeminent export controlled and ITAR restricted forum in the United States to review and discuss advances in materials for extreme environments. The Conference started in the 1970s as a small informal gathering for government and industry to share information on programs and state-of-the-art technology. Attendance has grown to nearly 500 people while preserving this same objective to share needs and trends in high-temperature and extreme environment materials, and the latest information on advanced materials and manufacturing processes. The five-day conference program includes two to three parallel sessions per day on topics including thermal protection materials, ceramic matrix composites, carbon-carbon materials, ballistic technologies, hypersonics, and gas turbine engines. Attendees are engineers, scientists, managers, and operational personnel from the turbine engine, aviation, missiles and space, and protective equipment communities. These communities include the Navy, Air Force, Army, MDA, NASA, DARPA, FAA, DOE, engine manufacturers, missile and aircraft manufacturers, commercial space companies, and material and component suppliers. The Conference will be held in St. Augustine again for 2024! Participation is limited to U.S. Citizens and U.S. Permanent Residents only with an active DD2345 certification.
The 48th International Conference & Exposition on Advanced Ceramics & Composites (ICACC 2024) will be held from Jan. 28–Feb. 2, 2024, in Daytona Beach, Fla. It is a great honor to chair this conference, which has a strong history of being one of the best international meetings on advanced structural and functional ceramics, composites, and other emerging ceramic materials and technologies.
Venue ONLY ON-SITE @AZL Hub in Aachen Building Part 3B, 4th Floor Campus Boulevard 30 52074 Aachen Time: January 31st, 2024 | 11:00-16:00h (CET) This first constitutive session will shape the future of the workgroup. ✓ Insights into solutions for e.g. circularity, recycling, sustainability, end of life etc. ✓ Interactive exchange along the value chain to tackle these challenges: Share your input in the “World Café” workshop session! ✓ Are you a solution provider? Take your chance and present your solution approach in a short 5-minute pitch. Get in touch with Alexander.
The Transformative Vertical Flight (TVF) 2024 meeting will take place Feb. 6–8, 2024 in Santa Clara, California, in the heart of Silicon Valley and will feature more than 100 speakers on important progress on vertical takeoff and landing (VTOL) aircraft and technology.
The EPTA – European Pultrusion Technology Association in cooperation with the American Composites Manufacturers Association (ACMA) invites you to the 17th World Pultrusion Conference which takes place on 29 February – 1 March 2024 in Hamburg, Germany. Visit the most important event in Europe in the market for pultruded fiber reinforced materials This conference takes place every two years and is the meeting point of the European and worldwide Pultrusion Industry. More than 25 international speakers from Finland, Belgium, Germany, France, Spain, The Netherlands, Turkey, UK, USA, Canada and others will present practical presentations about innovative applications, technologies and processes. Equally current market trends and developments are on the agenda. This World Pultrusion Conference takes place again in the week before the JEC World Composites Show (5-7 March 2024, Paris). The presentation language will be English. Please finde here the full program and booking opportunities. We appreciate very much welcoming you in Hamburg! Inquiries should be requested by email: info@pultruders.com
The Program of this Summit consists of a range of 12 high-level lectures by 14 invited speakers only. Topics are composite related innovations in Automotive & Transport, Space & Aerospace, Advanced Materials, and Process Engineering, as well as Challenging Applications in other markets like Architecture, Construction, Sports, Energy, Marine & more.
Thousands of people visit our Supplier Guide every day to source equipment and materials. Get in front of them with a free company profile.
Jetcam’s latest white paper explores the critical aspects of nesting in composites manufacturing, and strategies to balance material efficiency and kitting speed.
Arris presents mechanical testing results of an Arris-designed natural fiber thermoplastic composite in comparison to similarly produced glass and carbon fiber-based materials.
Cevotec, a tank manufacturer, Roth Composite Machinery and Cikoni, have undertaken a comprehensive project to explore and demonstrate the impact of dome reinforcements using FPP technology for composite tanks.
Initial demonstration in furniture shows properties two to nine times higher than plywood, OOA molding for uniquely shaped components.
The composite tubes white paper explores some of the considerations for specifying composite tubes, such as mechanical properties, maintenance requirements and more.
Foundational research discusses the current carbon fiber recycling landscape in Utah, and evaluates potential strategies and policies that could enhance this sustainable practice in the region.
JEC World 2024: Flax fiber producer Groupe Depestele and sustainable composites company Greenboats demonstrate flax fiber materials, demonstrators and product offer Circular Structures.
Acrylonitrile to be used in Tenax uses waste and residue from biomass-derived products or recycled raw materials that are ISCC Plus certified, maintaining same performance properties as conventional-based products.
JEC World 2024: Swancor demonstrates its EzCiclo recyclable epoxy and recycling process in wind, sporting goods and automotive applications.
Alliance for European Flax-Linen and Hemp has partnered with ecoinvent to enable a more comprehensive and transparent inventory database for the environmental impact of natural fiber-based products, services.
Online industry event in spring 2024 will feature six presentations covering sustainability in the composites industry.
Austrian research institute Wood K plus makes 95% silicon carbide ceramics more sustainable (>85% bio/recycled content), enables 3D shapes via extrusion, injection molding and 3D printing.
Explore the cutting-edge composites industry, as experts delve into the materials, tooling, and manufacturing hurdles of meeting the demands of the promising advanced air mobility (AAM) market. Join us at CW Tech Days to unlock the future of efficient composites fabrication operations.
During CW Tech Days: Thermoplastics for Large Structures, experts explored the materials and processing technologies that are enabling the transition to large-part manufacturing.
CW’s editors are tracking the latest trends and developments in tooling, from the basics to new developments. This collection, presented by Composites One, features four recent CW stories that detail a range of tooling technologies, processes and materials.
Closed mold processes offer many advantages over open molding. This knowledge center details the basics of closed mold methods and the products and tools essential to producing a part correctly.
The composites industry is increasingly recognizing the imperative of sustainability in its operations. As demand for lightweight and durable materials rises across various sectors, such as automotive, aerospace, and construction, there is a growing awareness of the environmental impact associated with traditional composite manufacturing processes.
CompositesWorld’s CW Tech Days: Infrastructure event offers a series of expert presentations on composite materials, processes and applications that should and will be considered for use in the infrastructure and construction markets.
In the Automated Composites Knowledge Center, CGTech brings you vital information about all things automated composites.
This CW Tech Days event will explore the technologies, materials, and strategies that can help composites manufacturers become more sustainable.
CompositesWorld’s CW Tech Days: Infrastructure event offers a series of expert presentations on composite materials, processes and applications that should and will be considered for use in the infrastructure and construction markets.
Explore the cutting-edge composites industry, as experts delve into the materials, tooling, and manufacturing hurdles of meeting the demands of the promising advanced air mobility (AAM) market. Join us at CW Tech Days to unlock the future of efficient composites fabrication operations.
Thermoplastics for Large Structures, experts explored the materials and processing technologies that are enabling the transition to large-part manufacturing.
Explore the technologies, materials, and strategies that can help composites manufacturers become more sustainable.
A report on the demand for hydrogen as an energy source and the role composites might play in the transport and storage of hydrogen.
This collection features detail the current state of the industry and recent success stories across aerospace, automotive and rail applications.
This collection details the basics, challenges, and future of thermoplastic composites technology, with particular emphasis on their use for commercial aerospace primary structures.
This collection features recent CW stories that detail a range of tooling technologies, processes and materials.
CAMX 2023: Kent Pultrusion is displaying its turnkey ServoPul servo-driven pultrusion lines and secondary equipment for handling composite profiles.
Kent Pultrusion (Kent, Ohio, U.S.), founded more than a decade ago, specializes in innovative pultrusion technologies, with more than 30 pultrusion lines installed worldwide. A division of MNM Manufacturing Inc., the company is uniquely established with the support of sister companies like Kent Automation and Criterion Machinery Co., all of which contribute to Kent’s ability to manufacture state-of-the-art ServoPul pultrusion lines and secondary equipment.
Kent Pultrusion’s ServoPul machines introduce servomotor and drive technology into the pultrusion process. These modern technologies enable electric, high-precision control of pulling and clamping forces, feedback monitoring registered to the operating system and an HMI that efficiently provides PLC controls.
The machines have operator interactive die-mounting systems, zero backlash couplings for added precision and flying cut-off saw capabilities that travel and cut at the product line’s speed. Additionally, there are safety interlocks in place for initiating machine shutdowns and immediate disengagement of the clamping process. All of these factors are standard specifications for Kent’s pultrusion lines.
The turnkey pultrusion systems are manufactured for flat sheet, structural, complex and custom processing solutions. The ServoPul design is specialized at handling pultruded profiles made of composite materials, consisting of synthetic organic resins composed of long fibers and mats, and glass fiber- and carbon fiber-reinforced polymers. ServoPul lines service a multitude of industries, including roofing, fiberglass floor plate, window configurations, as well as applications in construction, utilities, municipal facilities and more.
Moreover, the company’s team of first-class engineers, control specialists and assembly specialists have been built to deliver the best possible results through rigorous testing, case studies and boots-on-the-ground field service and installations. Kent Pultrusion also highlights its customer service and support opportunities to satisfy all challenge manufacturing needs.
Eighth-generation vehicle sports more composites, and features parts produced using unique materials and processes.
Fiber-reinforced plastic (FRP) replacing coated steel in more reinforced-concrete applications.
There are numerous methods for fabricating composite components. Selection of a method for a particular part, therefore, will depend on the materials, the part design and end-use or application. Here's a guide to selection.
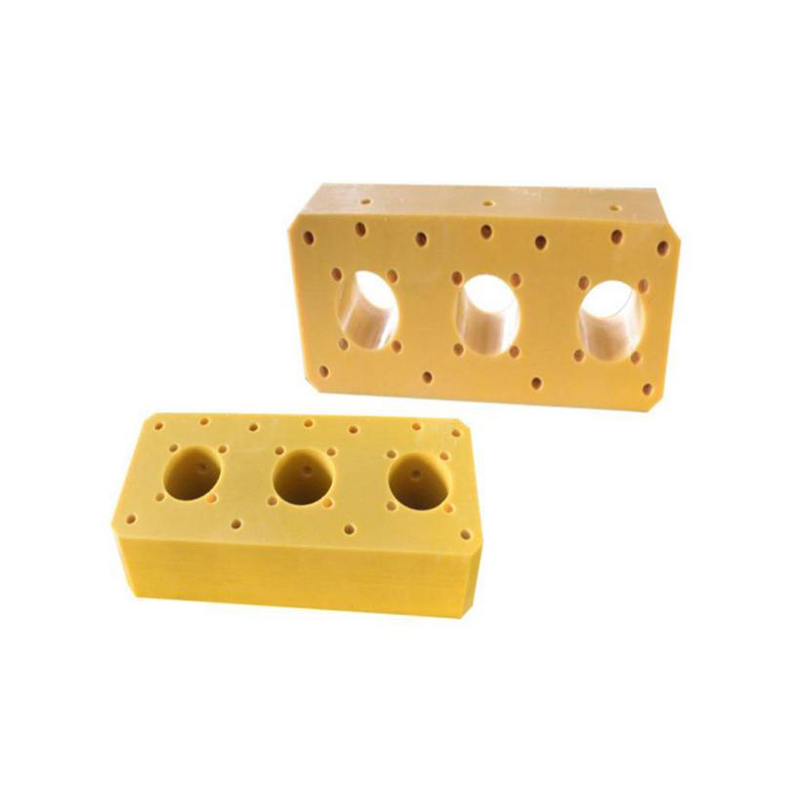
Insulation Profile CompositesWorld is the source for reliable news and information on what’s happening in fiber-reinforced composites manufacturing. Learn More